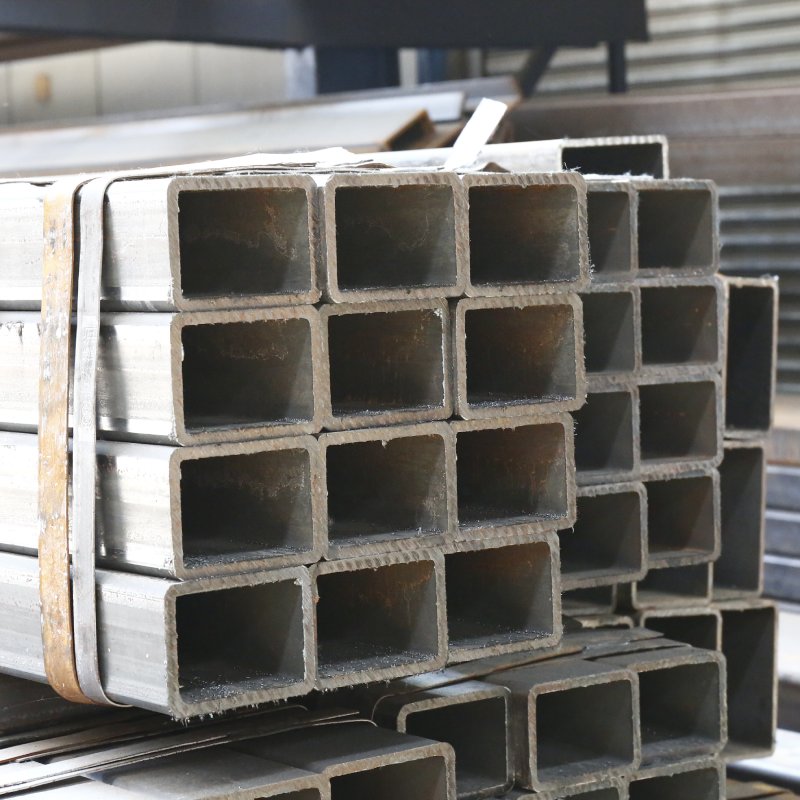
Image source Aiweiblockmachine
Adopting Predictive Maintenance Strategies for Long-Term Efficiency in Block Production Equipment
Title: Prolonging Efficiency: Adopting Predictive Maintenance Strategies for Long-Term Success in Block Production Equipment
Introduction:
In the ever-evolving landscape of block manufacturing, the efficiency and reliability of production equipment play a pivotal role in overall operational success. Traditional maintenance approaches, while essential, are gradually being augmented by advanced predictive maintenance strategies. This article delves into the importance of predictive maintenance in block production, exploring its applications, benefits, and the steps involved in implementing a proactive maintenance framework.
Understanding Predictive Maintenance:
1. Definition: Predictive maintenance is a proactive maintenance strategy that leverages data, analytics, and advanced technologies to predict equipment failures before they occur. By continuously monitoring the condition of production equipment, manufacturers can schedule maintenance activities precisely when needed, minimizing downtime and optimizing operational efficiency.
2. Key Components:
- Data Collection: Predictive maintenance relies on data collected from various sensors and monitoring devices installed on production equipment. These sensors track key parameters such as temperature, vibration, lubrication levels, and energy consumption.
- Analytics: Advanced analytics, including machine learning algorithms, process the collected data to identify patterns, anomalies, and potential failure indicators. This predictive analysis allows for early detection of issues and the generation of actionable insights.
- Integration with Maintenance Systems: The insights generated by predictive maintenance systems are integrated with existing maintenance management systems to facilitate timely scheduling of maintenance activities.
Applications in Block Production Equipment:
1. Block-Making Machines: Predictive maintenance for block-making machines involves monitoring critical components such as molds, hydraulic systems, and vibration patterns. Early detection of issues, such as mold misalignment or hydraulic system wear, allows for timely intervention to prevent equipment failure.
2. Curing Systems: Efficient curing is essential for the strength and quality of concrete blocks. Predictive maintenance in curing systems involves monitoring temperature and humidity levels, ensuring optimal conditions for the curing process. Any deviations can trigger early maintenance actions.
3. Material Handling Equipment: Material handling equipment, including conveyors and forklifts, is vital in the block production process. Predictive maintenance in this context involves monitoring wear on conveyor belts, lubrication levels, and the performance of motors to prevent unexpected breakdowns.
4. Energy-Efficient Kilns: Kilns are energy-intensive components in block production. Predictive maintenance for kilns includes monitoring combustion efficiency, refractory wear, and temperature profiles. Timely maintenance interventions ensure energy efficiency and prolonged kiln lifespan.
5. Packaging and Palletizing Systems: Ensuring the efficiency of packaging and palletizing systems is crucial for the final stage of block production. Predictive maintenance involves monitoring robotic systems, sensors, and conveyor systems to prevent malfunctions that could disrupt the packaging process.
Benefits of Predictive Maintenance in Block Manufacturing:
1. Minimized Downtime: Early detection of potential equipment failures allows for scheduled maintenance activities, minimizing unplanned downtime. Predictive maintenance ensures that production equipment is consistently operational, contributing to increased overall efficiency.
2. Cost Savings: Proactive maintenance reduces the need for emergency repairs and replacements, resulting in cost savings. By addressing issues before they escalate, manufacturers can optimize maintenance budgets and allocate resources more effectively.
3. Extended Equipment Lifespan: Timely interventions and optimized maintenance activities contribute to the extended lifespan of production equipment. By addressing wear and tear proactively, manufacturers can maximize the return on their capital investments in machinery.
4. Enhanced Safety: Predictive maintenance helps identify and address safety-related issues before they become critical. This proactive approach contributes to a safer working environment for employees, reducing the risk of accidents and injuries.
5. Improved Product Quality: Production equipment operating at optimal conditions ensures consistent and high-quality block production. Predictive maintenance contributes to maintaining the precision and reliability of equipment, directly impacting the quality of the final product.
6. Energy Efficiency: Monitoring and optimizing equipment performance through predictive maintenance contribute to energy efficiency. By addressing issues such as inefficient combustion in kilns or malfunctions in motors, manufacturers can reduce energy consumption and environmental impact.
Steps to Implement Predictive Maintenance in Block Manufacturing:
1. Equipment Assessment: Conduct a comprehensive assessment of production equipment to identify critical components and potential failure points. This involves understanding the specific maintenance requirements of each machine in the block production process.
2. Sensor Installation: Install sensors and monitoring devices on key components of production equipment. These sensors should be capable of collecting data on relevant parameters, such as temperature, vibration, lubrication levels, and energy consumption.
3. Data Collection and Analysis: Establish a data collection and analysis framework to process the information gathered by sensors. Implement advanced analytics, including machine learning algorithms, to identify patterns, anomalies, and early indicators of potential equipment failures.
4. Integration with Maintenance Systems: Integrate the predictive maintenance system with existing maintenance management software. This ensures seamless communication and coordination between the predictive maintenance insights and the scheduling of maintenance activities.
5. Establish Thresholds and Alarms: Define thresholds for key parameters based on which alarms and alerts are triggered. These thresholds should be set to indicate potential issues well before they escalate to the point of causing equipment failure.
6. Continuous Monitoring and Calibration: Implement continuous monitoring of production equipment and regularly calibrate sensors to ensure accuracy. This involves periodic checks and adjustments to maintain the reliability of the predictive maintenance system.
7. Staff Training: Train maintenance and operations staff on the utilization of predictive maintenance tools and insights. Developing in-house expertise ensures that the team can effectively interpret data, respond to alarms, and perform scheduled maintenance activities.
8. Documentation and Reporting: Establish a documentation and reporting system to track the performance of production equipment over time. This historical data provides valuable insights for continuous improvement and optimization of predictive maintenance strategies.
Challenges and Considerations:
1. Initial Investment: Implementing predictive maintenance involves an initial investment in sensors, monitoring devices, and analytics software. While the long-term benefits are significant, manufacturers should carefully evaluate the costs and returns associated with the implementation.
2. Data Security and Privacy: Ensuring the security and privacy of data collected from production equipment is crucial. Manufacturers must implement robust cybersecurity measures to protect sensitive information from unauthorized access or cyber threats.
3. Cultural Shift: Adopting predictive maintenance requires a cultural shift within the organization. Employees need to embrace the proactive mindset of addressing potential issues before they impact production. Communication and training are essential for fostering this cultural change.
4. Integration with Existing Systems: Integrating predictive maintenance systems with existing equipment and software can be complex. Compatibility issues may arise, and manufacturers should carefully plan and execute the integration process to avoid disruptions in operations.
5. False Alarms: Setting thresholds too sensitively can lead to false alarms, causing unnecessary interruptions in production. Finding the right balance between early detection and minimizing false alarms is essential for the effectiveness of predictive maintenance.
Case Studies: Successful Implementation of Predictive Maintenance in Block Manufacturing
- Reducing Downtime in Block-Making Machines: Case Study: A block manufacturing plant implemented predictive maintenance on its block-making machines. By monitoring vibration patterns and lubrication levels, the plant reduced unplanned downtime by 30%, leading to increased overall efficiency and cost savings.
- Optimizing Kiln Performance: Case Study: A block production facility integrated predictive maintenance into its kiln system. By monitoring combustion efficiency and refractory wear, the facility optimized kiln performance, resulting in a 20% reduction in energy consumption and extended kiln lifespan.
Future Trends and Developments:
1. Internet of Things (IoT) Integration: The integration of IoT devices and connectivity will further enhance the capabilities of predictive maintenance. Real-time data from interconnected devices will provide more comprehensive insights and enable more proactive decision-making.
2. Artificial Intelligence (AI) Advancements: AI technologies, including advanced machine learning algorithms, will continue to evolve. These advancements will enhance the accuracy of predictive maintenance models, enabling more precise predictions and actionable insights.
3. Augmented Reality (AR) for Maintenance Assistance: AR technologies can be leveraged to provide maintenance personnel with real-time information and guidance. This includes overlays of equipment status, maintenance procedures, and troubleshooting guidance, enhancing the efficiency of maintenance activities.
Conclusion:
In the competitive landscape of block manufacturing, where operational efficiency is paramount, predictive maintenance emerges as a game-changer. By adopting a proactive approach to equipment maintenance, manufacturers can minimize downtime, reduce costs, and ensure the longevity of their production assets. As the industry continues to embrace technological advancements, predictive maintenance stands as a key strategy for achieving long-term success and sustainability in block production.