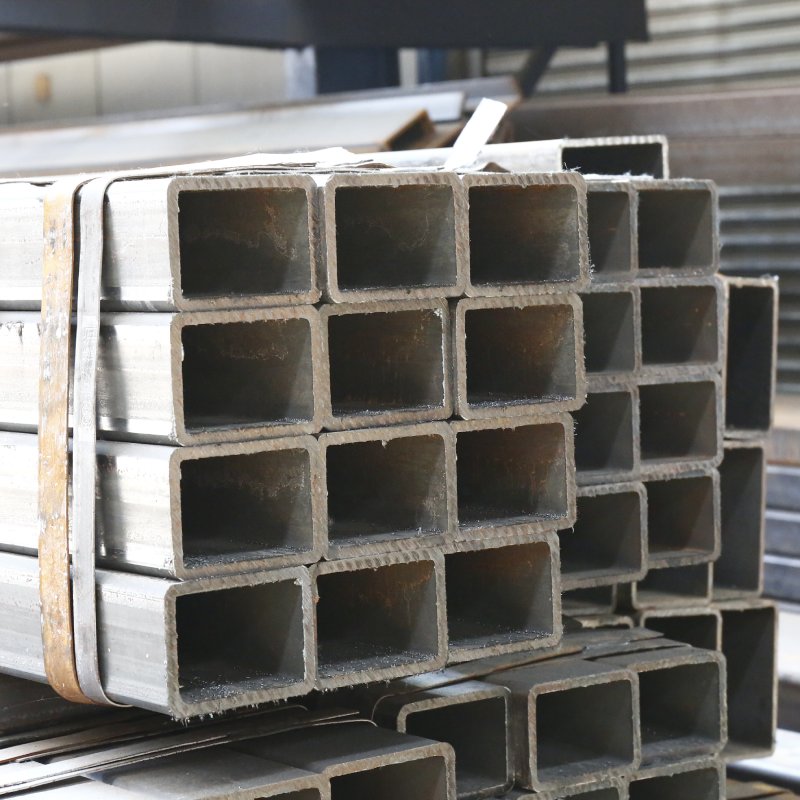
Image source Aiweiblockmachine
Title: Strategies for Implementing Smart Manufacturing in Full-Automatic Block Production
Introduction
In the rapidly evolving landscape of manufacturing, smart technologies have become integral to improving efficiency, reducing costs, and enhancing overall productivity. In the realm of block production, the integration of smart manufacturing practices is revolutionizing the way operations are conducted. Full-automatic block production, with its potential for increased precision and reduced human intervention, is an ideal candidate for the implementation of smart manufacturing strategies. This article explores key strategies for incorporating smart manufacturing into full-automatic block production processes.
1. **IoT Integration for Real-Time Monitoring and Control**
One of the fundamental pillars of smart manufacturing is the Internet of Things (IoT). By integrating sensors and connected devices throughout the production line, manufacturers gain real-time insights into various aspects of the process. In the context of full-automatic block production, sensors can monitor equipment performance, temperature, humidity, and other critical variables. This data is then transmitted to a centralized system, allowing for immediate analysis and adjustments.
Real-time monitoring enables proactive maintenance, reducing downtime and preventing potential issues before they escalate. For example, if a machine begins to show signs of wear, IoT sensors can trigger a maintenance alert, prompting timely intervention. This predictive maintenance approach not only enhances equipment lifespan but also ensures continuous and uninterrupted production.
2. **Data Analytics for Process Optimization**
The massive amounts of data generated by smart manufacturing systems are a valuable resource when leveraged effectively. Data analytics tools can sift through this information to identify patterns, trends, and areas for improvement. In full-automatic block production, data analytics can optimize the manufacturing process by analyzing factors such as production speed, energy consumption, and raw material usage.
By understanding historical data, manufacturers can identify inefficiencies and bottlenecks in the production line. This insight enables strategic decision-making to streamline processes, enhance resource utilization, and improve overall operational efficiency. Furthermore, data analytics can contribute to product quality improvement by identifying correlations between production parameters and the final product’s characteristics.
3. **Machine Learning for Predictive Quality Control**
Smart manufacturing goes beyond automation; it involves the application of advanced technologies such as machine learning (ML) to refine and enhance processes. In the context of full-automatic block production, ML algorithms can be employed for predictive quality control. By analyzing historical data and correlating it with product quality outcomes, machine learning models can predict potential defects or deviations from quality standards.
This predictive quality control approach allows manufacturers to take corrective actions in real-time, minimizing the production of faulty blocks. ML algorithms can continuously learn and adapt, improving their accuracy over time and contributing to a consistent and high-quality end product. This not only reduces waste but also enhances customer satisfaction by delivering products that meet or exceed quality expectations.
4. **Robotics for Flexible and Efficient Production**
The integration of robotics is a cornerstone of full-automatic block production. Smart manufacturing takes this a step further by incorporating advanced robotics that can adapt to changing production requirements. Flexible robotic systems can handle various tasks, from material handling to precise assembly, with minimal reprogramming.
In a smart manufacturing environment, robotics are equipped with sensors and connectivity, allowing them to collaborate seamlessly with other machines and systems. This interconnectedness enables dynamic adjustments to the production process based on real-time data. For example, if there is a sudden increase in demand, the robotic system can optimize its workflow to meet production targets efficiently.
5. **Cybersecurity Measures for Data Protection**
As manufacturing processes become more interconnected, the need for robust cybersecurity measures becomes paramount. Protecting sensitive data and ensuring the integrity of smart manufacturing systems is crucial to prevent potential disruptions and unauthorized access. In the context of full-automatic block production, where proprietary formulas and production algorithms are at play, cybersecurity measures are non-negotiable.
Implementing secure communication protocols, regularly updating software and firmware, and conducting cybersecurity audits are essential components of a comprehensive cybersecurity strategy. Manufacturers must prioritize the protection of intellectual property, production data, and other critical information to maintain a secure and resilient smart manufacturing ecosystem.
6. **Employee Training and Collaboration**
While smart manufacturing aims to automate and optimize processes, human involvement remains crucial. Employees play a vital role in overseeing, maintaining, and optimizing smart manufacturing systems. Therefore, comprehensive training programs are essential to equip the workforce with the skills required to operate and troubleshoot advanced technologies.
Moreover, fostering a culture of collaboration between humans and machines is imperative. Employees should be encouraged to work alongside automated systems, leveraging their expertise to enhance the overall efficiency of the production process. This collaborative approach ensures that the implementation of smart manufacturing not only improves operational outcomes but also creates a positive and empowering work environment.
Conclusion
The integration of smart manufacturing strategies in full-automatic block production holds the promise of increased efficiency, enhanced quality, and reduced operational costs. By leveraging IoT, data analytics, machine learning, robotics, and cybersecurity measures, manufacturers can transform their production processes into intelligent, adaptive, and interconnected systems. As the industry continues to evolve, embracing these strategies will be essential for staying competitive and meeting the demands of a rapidly changing market. Full-automatic block production, when infused with smart manufacturing technologies, becomes a cornerstone of innovation, setting new standards for precision, quality, and sustainability in the manufacturing sector.